NC Transform
Adaptive Machining Software for the modern factory
NCT is the solution you have been looking for to sustain a competitive edge in the future.
Use your existing processes, machines, fixtures, and programming in conjunction with NCT. Over night, you will see simplified setups, increased accuracy, elimination of rework, and the ability to achieve first run quality.
Using NCT, you’ll be able to create more demanding setups, giving you the ability to bid, win, and profit from work which you would otherwise have to pass up.
NC Transform & the F-35 Engine
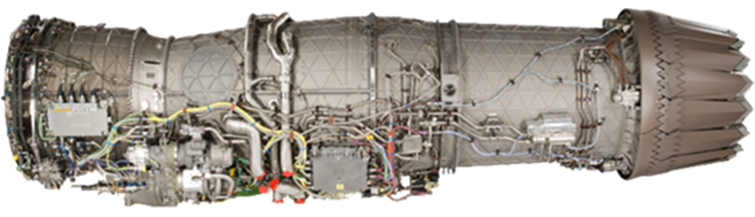
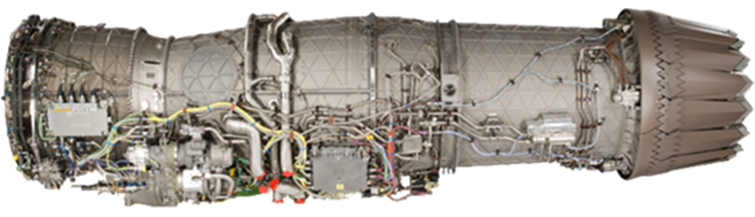
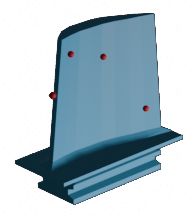
In the case of the F-35 stators, NCT uses touch probe data from the air flow surfaces and morphs the tool path of the mounting surfaces process to achieve first run quality without the need for complex fixturing or lengthy setup processes.
In the case of the F-35 flaps, NCT uses touch probe data from one side and creates a full 6 DOF alignment for the tool paths on the opposite side of the part.
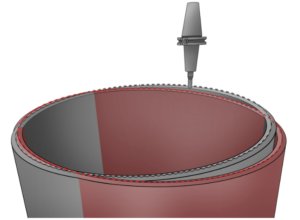
See how NCT is currently automatically setting countersink depths to the freeform surface of these cowlings.
NC Transform's Iterative Alignment Simplifies Fixturing
With NC Transform it does not matter if every part from the casting house, forge shop, or carbon fiber layup facility is a complete snowflake. NCT will adjust to the reality of your process. Using measurements to discover the actual locations of your part’s datums when fixtured on the machine and adapting your part program accordingly.>
NCT creates a pathway for difficult parts to successfully move from raw material to perfect assembly, making NCT a valuable tool for manufacturers.
Individual Feature Alignment
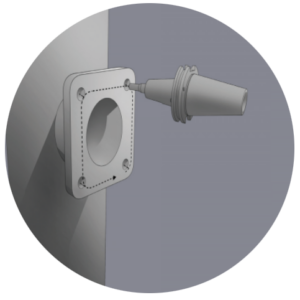
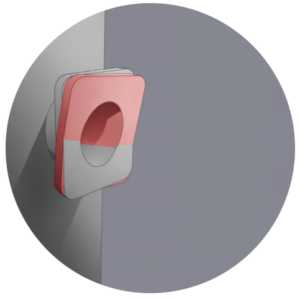
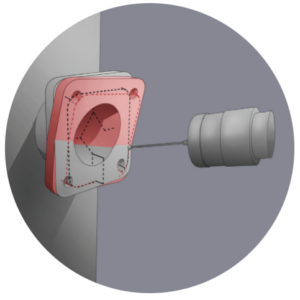
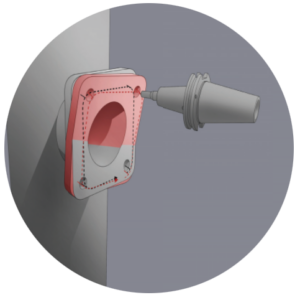
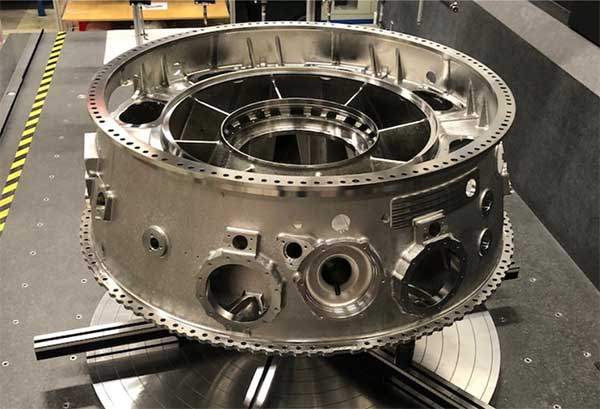
Tool Path Morphing
Small Features on Big Parts
Adding a chamfer to a large round part can be extremely challenging. If the chamfer is only 3/8″ and the part is out of round by just 1/4″, the chamfer will never be accurate. It could end up being undersized, or oversized, or it may not even be possible to achieve. However, with NC Transform, you can measure a spline of data around the edge of the part and watch the software morph the tool path to follow the real edge, resulting in a precisely machined part.
Blending on Forged, Cast, or Repair Parts
NC Transform enables direct measurement of part surfaces on the machine and adapts tool paths to blend and morph to follow the complex topology of airfoil surfaces. This allows for the smooth removal of casting gates, seamless weld repairs, and automatic blending of welded-on tips and leading edges, eliminating the need for extensive hand blending.
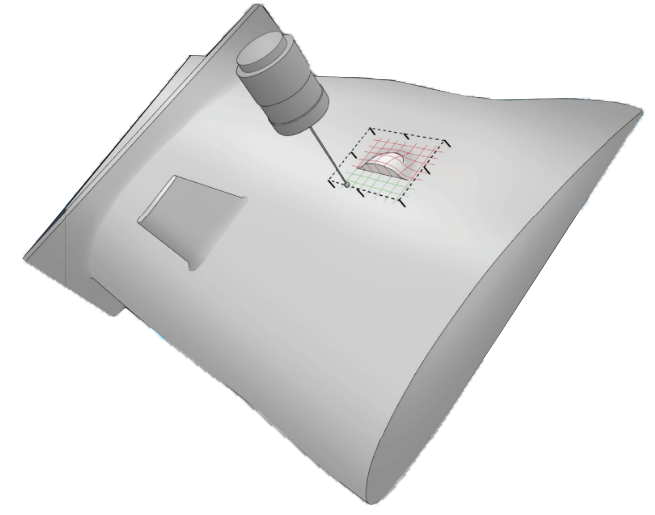
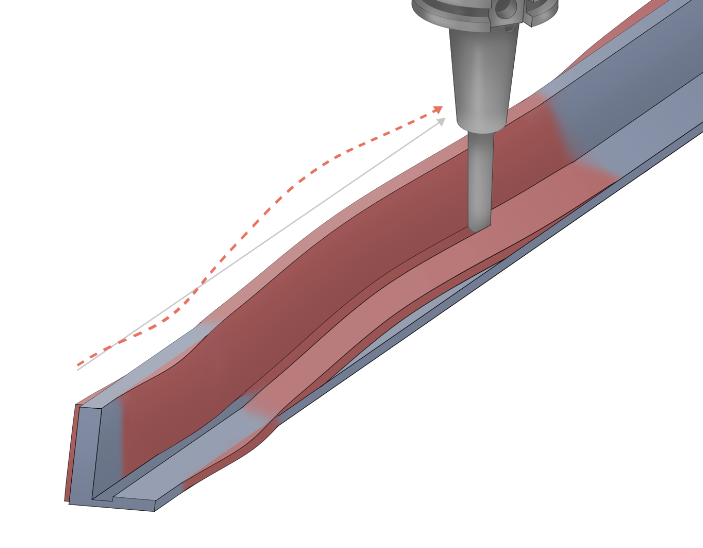
Long Stringers, Beams, and Spars
NC Transform can adapt to the challenge of cutting even the most mishappen parts. Long and slender parts often pose challenges due to their lack of rigidity and tolerance requirements. With the ability to measure cross-sections along the length of the part, NC Transform can adjust the tool path to match the actual position of the part on the machine, rather than relying on the theoretical position from the CAM software. This ensures that tight tolerances are consistently maintained, without the need for excessive manual intervention or rework.
Let’s face it, human error is unavoidable.
Our software all but eliminates human error with its adaptive machining capabilities.
Eliminate Human Error:
Let's face it, human error in manufacturing can be a problem. Maybe something isn't set properly in the fixture, or the wrong program / tool is selected. It's costly, but also a thing of the past when running NCT.
Best Fit Technology:
Irregular part? Mis-aligned part? NCT will ensure your parts turn out right the first time, or it won’t let the cut program start.
Eliminate Re-work:
Yes, we said eliminate re-work. NCT is more than an offset system, it truly adapts to what is presented on the machine and produces a compliant part.
User Friendly:
After NCT is setup in your shop, it usually only takes a short training session for the NC programmers and the operators to become a fully integrated part of your process.
Even mild errors can cost tens of thousands of dollars (or more!). With NCT’s advanced algorithms, you don’t have to accept expensive errors as just “part of the process.” It adapts your existing process to accommodate for mis-aligned materials and irregular or misshapen parts. This all means that you get a compliant part, every time, with no mistakes.
Costly mistakes are a thing of the past when running NCT.
Why choose us
What Makes NC Transform Different?
Ease of Use
Our user-friendly interface means this program truly does take the headache out of automating your factory. State of the art doesn’t have to mean confusing or complicated when you choose NCT for your Industry 4.0 factory.
Platform Independent
Unlike other adaptive platforms, NCT does not rely on your CAD/CAM software. Consequently, your current programming process is compatible with NCT. You probably don’t have a factory dedicated to one specific machine tool builder. NCT runs on any machine, making this a non-issue for your smart factory.
Cost of Implementation is Low
Especially when compared against the cost of mistakes, complicated fixtures, and rework, implementing this software is affordable and convenient. Unlike other adaptive platforms, NCT does not require the purchase of additional machine cycles. View our case studies and see for yourself.
Quick & Convenient Installation
It doesn’t take days, weeks, or months to take your factory to the next level. You don’t even have to do it yourself. We come to you and install, demonstrate, and train your team.
What is Adaptive Machining?
To learn more about our adaptive machining, click on the link below to view a comprehensive PDF.
Works With Any
- Controller
- Machine
- CAD/CAM System
- Probe
Benefits Include
- Elimination of need to shim parts into place
- Eliminate the need for expensive fixturing
- Save significant time in on-machine setup for each part run
- Eliminate rework
- Increase geometric accuracy
- Increase shop’s overall capabilities
- Reduce or eliminate scrap parts
- Ability to probe at multiple vectors
- Easy to learn software doesn’t make you change your process
- Rapid ROI
Additional Benefits & Add-Ons
Feature Correction
We’re proud of our Feature Correction add-on because it’s what every Industry 4.0 factory strives for: true machine learning for continual improvement in each part. Feature Correction is a closed-loop machining system, learning from each CMM inspection and ensuring that each part is better with every run.
On Machine Inspection
On Machine Inspection is a valuable add-on to our NCT Software. This intelligent software allows parts to be inspected while they’re still on the machine, eliminating unnecessary labor and downtime.
NCTC (Cutter Comp)
Discover NCTC (Cutter Comp), a complete 6 Degree of Freedom cutter diameter compensation system compatible with all machines in your workshop. With NCTC, achieve reliable results without the frustration of error codes that commonly affect other systems. Click here to reach out for an online demonstration and receive an ROI estimate.
Why NCSS Tool Compensation Succeeds Where Others Fail
Cutter Compensation with NC Software’s NCTC saves in overall cutter cost. However, savings alone are not enough if parts are damaged or scraped in the process. Our advanced algorithms deliver a true 3-5 axis compensation for all your machines. Say goodbye to technical complications, operator training issues, and costly errors that have prevented this simple process to lower tool expenditures. NCTC system removes operator involvement, and variation between machine and control combinations. NCTC does not use machine control algorithms so there is no special programming required. Use the G code you currently have, and begin saving on machining costs.